The number and selection of blocks used in a specific project are determined by the end result envisioned by the designer. A fixed arm, for instance, or an automatic elevator doesn’t need wheels or legs. A head with electronic eyes programmed to “see” and detect things doesn’t need arms. The common blocks used in all the projects are as described below.
Control
This is the “brain” of any project in a robotic or mechatronic system. All the electric parts of a robot or any other project are controlled by electronic circuits.
The basic controls for robots and mechatronic projects are as follows.
(a) Position control. Arms with grips or other object manipulators must have precise controls to place them in the correct position. The movement of a head with eyes is controlled by a one-axis control block.
(b) Kinematic control. Any project with moving parts needs this kind of control.
The speed of any moving part must be precisely determined and controlled by the circuits. One of the most important of the controls in this group governs the speed of the motor that moves a robot
(c) Dynamic control. Many parts of a robot or mechatronic project incorporate forces that must be controlled during operation. When the grip of a robot manipulates an object, its necessary to use some kind of control that determines what degree of force is necessary to grasp the object firmly without breaking it. A real challenge for the project builder is to build a robot grip that can take an egg from one basket and put it in another without breaking it. Such tasks require precise dynamic control.
(d) Adaptive control. Adaptive control is needed when a function of a robot or mechatronic device must change during the execution of a process. An example is the need for increased grip force when pressing against a spring.
More force is required as the spring is compressed. Another example of adaptive control is the application of more power to a motor to maintain a constant speed, as when a robot moves from level ground to an incline or when it must move a heavy object.
(e) External control. External controls are used when a human operator is used to command all the tasks of a robot. The human is the “brain,” and it uses such sensors (senses) as vision in the control of the robot’s operations.
To transfer commands for a robot or mechatronic device, the operator can use a variety of “interfaces.” The basic options are links that employ radio, infrared (IR), wires, and even voice commands. Modern projects can include voice recognition circuits to receive orders directly from an operator. A computer can also be used to interface the control unit and the robot or mechatronic device.
At this point, is important to consider the degree of intelligence that may exist in a robot. Complex controls can give an observer the false impression that the robot is “intelligent.” However, a control block that employs many functions is not an intelligent block. Intelligence can be added if the robot must make decisions based in input from its own sensors or from an operator who employs a specific data input block.
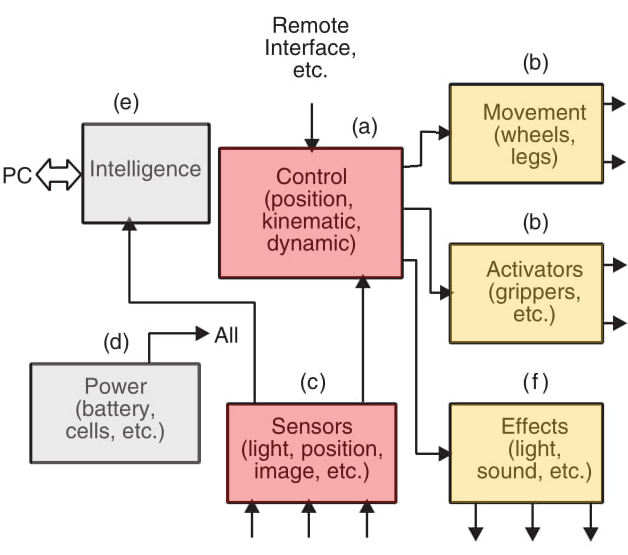
Actuators
Robots and mechatronic machines must have some way to manipulate objects or perform some kind of action in the external world. As outlined below, many types of actuators are found in practical projects.
Movement.
Robots can move from one place to other using legs, wheels, or tracks. The legs can be moved using motors, solenoids, or shape memory alloys* (SMAs).
Manipulation.
Robots and mechatronic devices don’t have hands. They use grippers to manipulate objects, and these grippers are controlled by electronic circuits. The movement of the grippers can be driven with solenoids, motors, or SMAs. Figure 2 shows some types of grippers.
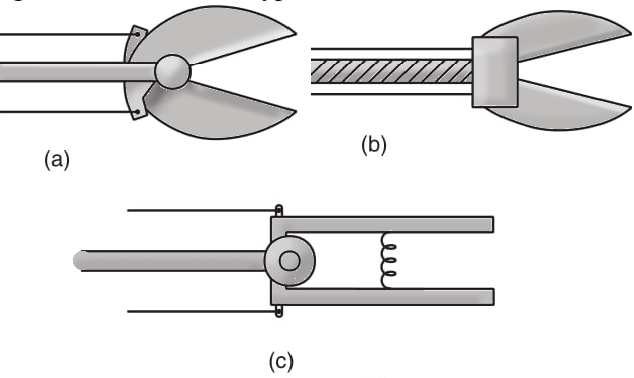
Manipulation can also be effected using equipment that is specially designed for a specific task, as we see in many industrial robots. In many applications, mechanically coupled parts can be adapted to fit the size and shape of whatever object must be manipulated. This is suggested by Figure 1.3.
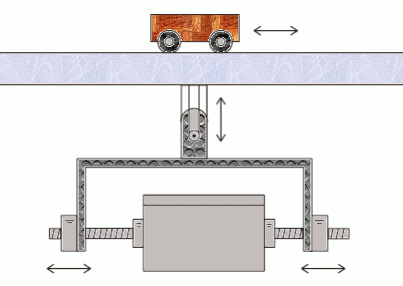
Sensors
Robots and mechatronic devices detect what happens in the real world using sensors. The sensors are very important, since they can transmit information about the position of a robot or an arm, the size and shape of an object being manipulated, the presence of obstacles (if it is a moving robot), and much other information, including the object recognition by size and shape, as found in some “intelligent” projects.
A TV camera can be linked to an intelligent circuit, thus allowing an automatic arm to select pieces that have a specific size and shape from among many mixed pieces as shown.by figure 4.
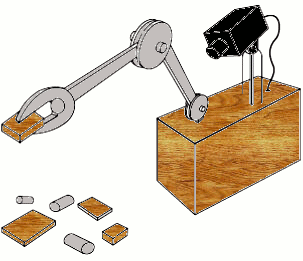
The basic sensors found in projects of robotics and mechatronics are as follows:
Light: Light-dependent resistors (LDRs, e.g., CdS cells or photoresistors), photodiodes, photo cells, and phototransistors
Pressure: conductive foam, electromechanical sensors, semiconductor sensors
Temperature: NTC (**), PTC, diodes, or transistors
Image: Charge-coupled devices (CCDs), photodiodes, or phototransistor matrices
Position: potentiometers, sonar, radar, infrared (IR) sensors
Contact: microswitches, pendulums
Proximity: capacitive, inductive, or IR
Power
Any project involving electronics and moving parts needs some kind of electric power supply. If the project is a moving robot, it is ideal if you can put the power supply inside it. Batteries and cells can be used in this way. The size and the type of battery depends on the power needed by the robot, how long it must operate without recharging, and the tasks it must do.
If the device is fixed (e.g., a robotic arm) or relatively fixed (e.g., an elevator), electric power can be supplied by the ac power line. Since the electronic circuits and electromechanical devices used in the project usually use dc power, circuits that provide rectification, filtering, and voltage stabilization must be included if an ac power source is used. Alternative power sources, including solar cells, generators coupled to internal combustion engines, fuel cells, and many others, can be employed in some projects.
Intelligence
This is in important block that is used in many mechatronics and robotics projects. Intelligence often can be considered as an independent block.
The intelligence blocks process information that is picked up by sensors or received from other external sources (e.g., a computer or the human operator) and make decisions about the tasks that the system must perform. The intelligence block can be as simple as a basic neural comparator that, for example, senses ambient light and determines the robot’s distance from the light source or a wall. It can also encompass much more complex configurations, involving highlevel decisions.
Two forms of artificial intelligence are suitable for applications in robotics and mechatronics:
Software intelligence
Software intelligence is provided by a computer, microprocessor, or microcontroller in which any intelligent software runs. Hardware links provide the data the processor needs to make decisions and communicate with the control block.
The decisions are programmed in a basic structure and in some cases can be changed according the incoming data. In such a case, the program can “learn” with experience, which is considered to be a basic characteristic of intelligent systems.
Programs that simulate neural networks are the preferred by students, researchers, and developers in the artificial intelligence field. Another important tool for the design of intelligent systems is fuzzy logic.
Software intelligence can be located inside the own robot or mechatronic machine when microprocessors and microcontrollers are used. The Arduin or BASIC Stamp® chip* provides a simple way to add some degree of intelligence to a machine. It can be programmed to take some decisions from the inputs of sensors of external control.
The experimenter can find many programs that simulate neural networks and fuzzy logic. Many can be used to add intelligence to computers, automatons, and other machines.
iv class="nota">** NTC = negative temperature coefficient, PTC = positive temperature coefficient. With an NTC device, resistance goes down as temperature increases. A PTC device works in the opposite manner.
Hardware intelligence
Another way to add intelligence to a machine is by using circuits that can learn. The basic idea is to imitate the way living beings process the information they receive via their senses, i.e., using the nervous system. The analogy is shown in Figure 5.
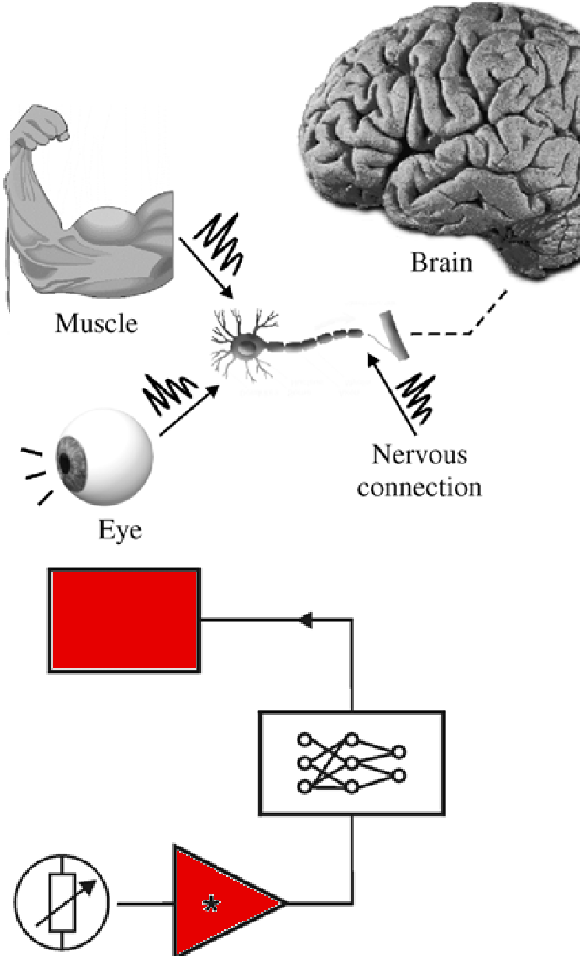
The living being receives the information from the external world by sensors coupled to nervous cells. The cells send the information to a brain, formed by a network of cells, where it is processed. The result is sent back to effectors (muscles, for instance) by another network of nervous cells.
Using artificial neurons, the designer can wire the elements together, forming neural networks that imitates the operation of the living being’s information processing system, adding some degree of intelligence to a robot.
Of course, a single electronic neuron can’t produce what we can define as an intelligent behavior. It is the behavior of an amoeba. Even using thousands or millions of neurons, the intelligence you will add to your project will not exceed that of a worm.
A neural network can learn and make decisions, making the machine somewhat intelligent. Neural networks in the form of integrated circuits can be bought from component dealers such as Mouser Electronics. Starting with ICs of this type, designers can create complex neuron networks with such capabilities as learning, decision making, and more.
Effects
Depending on the application, the robot or the mechatronic device must have some special means of getting people’s attention, or which may even simulate human behavior. In practical projects, we can consider including blocks that produce sounds, speak words or answer questions, produce light effects, or even provide a self-defense mechanism. Basically, the effects that can be used in these projects involving robotics and mechatronics are as follows:
Sounds: sirens, voice synthesis, heartbeat, breathing, etc. (The heartbeat and breathing are used in some dolls to add a bit of realism.)
Light effects: flashers, blinkers, stroboscopic signaling, etc.
Defense: high voltage